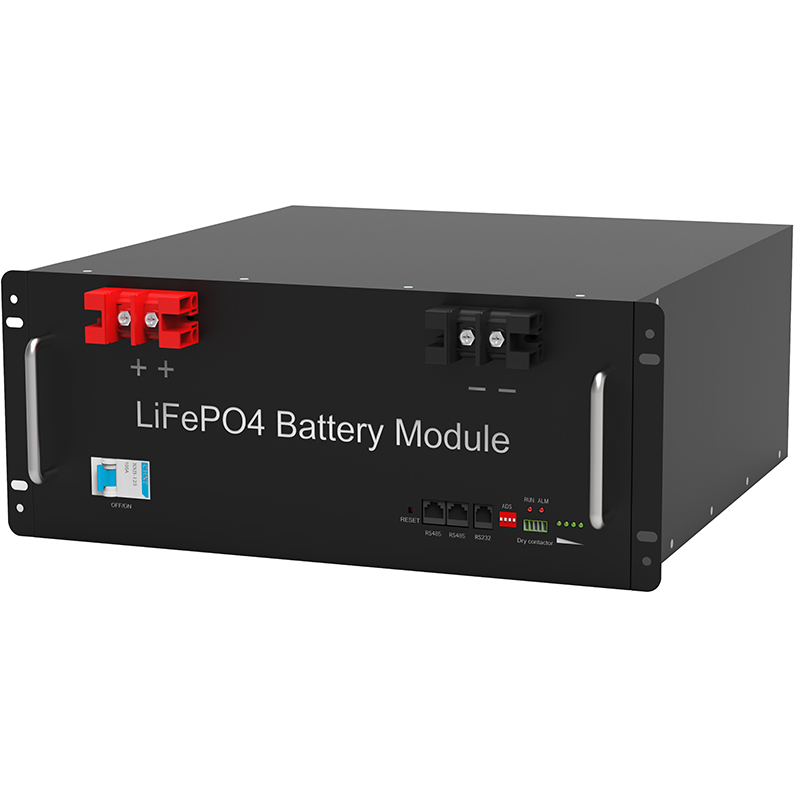
At present, most of the battery monitoring module is a voltage inspection instrument, and online monitoring of the battery is monitored, and the alarm is given when the set value is exceeded. Relative to the previously set voltage monitoring method, monomer voltage monitoring is a big step, but for the long-term operation of the battery, the problem of failure, the problem of voltage energy reflection is very limited: 100AH battery and The difference between the battery attenuated to 10ah is difficult to distinguish between the floating voltage. Therefore, it is necessary to discuss from the failure mode of the battery, thereby solving the monitoring of the battery.
Second, the failure mode of the valve control lead-acid battery
For valve-controlled lead-acid batteries, the usual performance deterioration mechanism has the following cases:
1, accumulation of heat
When the opening lead-acid battery is charged, in addition to the active substance regeneration, there is a step-by-step electrolysis of the water in the electrolyte to form hydrogen and oxygen. When the gas is covered from the battery out of the pores to the atmosphere, each 18 grams of water decomposes the heat of 11.7 kk.
For valve-controlled lead-acid batteries, the oxygen generated during charging flows to the negative electrode, and oxygen is oxidizing the active material sponge in the negative electrode plate, and effectively lows electrolysis and lost water. Since the oxygen circulation inhibits the precipitation of hydrogen, and oxygen is involved in the reaction and produces water. Thus, although the discharge problem of the explosive gas mixture is eliminated, this sealing has reduced thermal diffusion of an important way, but can only be the only way to heat through the heat transfer of the battery shell wall.
Therefore, the thermal out-of control problem of the valve-controlled lead-acid battery is a often encountered problem.
The valve-controlled lead-acid battery depends on the heat conduction of the wall wall to dissipate heat, and the battery is well ventilated and low room temperature is important. In order to further reduce the risk of thermal out-of control, the floating voltage is typically determined depending on the different producers and different room temperature. Manufacturers generally give the floating voltage and temperature compensation factor of the battery.
2, sulfate
The valve control is more likely to produce a negative electrode plate for sulfating. This is because:
1) Lower potential of the negative electrode plate caused by the cycle of oxygen;
2) The layers of the acid formed in the bottom of the battery collected in the strong acid electrolyte are difficult to avoid in this non-flow, non-cyclic electrolyte system.
Both of these may produce a certain number of residual sulfate under floating conditions, and then transit into a permanent sulfate form. Therefore, when the polar is accelerated, the capacity of the available discharge space available will be reduced. This situation will deteriorate with the increase in the temperature of the negative plate. Due to the occurrence of oxygen circulation, the surface of the negative plate is oxidized, and a considerable amount of heat release is released.
3, corrosion and falling off the positive plate group
In the valve-controlled lead-acid battery, this form of performance is even more serious. Due to the oxygen circulation reaction, the negative electrode active material is continuously oxidized to form sulfate, effectively maintains the discharge state, thus reducing the potential of the negative plate. The potential for a given floating voltage positive electrode group is correspondingly higher. Therefore, the oxidation atmosphere has exacerbated, causing more oxygen precipitation, which intensifies the corrosion and falling of the active substance.
4, the drying of the battery
The effective rate of the gas reconstructed mechanism during use is not 100%, and the water is electrolysis to form hydrogen and oxygen, although it is below 2% of the electrolysis rate of the rich liquid battery, but water will gradually lose.
When the loss of water is the main failure cause, the specific gravity of the electrolyte will increase, and when the specific gravity increases from the initial 1.30 to 1.36, the loss of loss of about 25% is indicated. When the loss of water reaches 25%, the high concentration of the acid accelerates sulfated, and the proportion of electrolyte has begun to fall. The battery voltage is directly proportional to the specific gravity of the electrolyte, so the battery voltage is not a reliable display of the battery health.
5, corrosion of lead in the upper lead
The corrosive corrosive corrosive in the lead-acid battery is originally in the various design of the lead-acid battery. In summary, the negative electrode plate is located at a highly reduced atmosphere, which is usually immersed in the electrolyte liquid level in the open cell, so that the erosion caused by oxygen from the positive electrode plate. . However, many of the valve-controlled batteries do not protect the polar plate ear, pole and bus bar, especially between the two welded joints. Therefore, they are exposed to escape from the oxygen circulation and in the continuous oxygen stream in the upper portion of the battery board. Depending on the consistency and production quality of the leaflet (tedles) and pole selected lead alloys (requiring the gate portion to completely dissolve the welding and the low porosity of the bus bar), rapid oxidation may occur.
Third, the development of battery monitoring system
In order to provide a good operating environment to the battery, online monitoring of the battery, BMS-Battery manufacturing system, is successful, and become a key part of a high reliable power system.
1, internal resistance measurement of battery cells
Internal resistance R is relatively than the cross-sectional area A of the transmission current. The sulfate and corrosion of the active substance, the sulfate and corrosion of the bus bar, and dryness can reduce effective cross-sectional area A, so it can detect the failure of the battery by measuring the internal block.
The degree of correlation between internal resistance and battery state varies greatly. From the relevance of reports, the variation ranges from 0% to 100%. British Electronics Association (ERA) has a large number of battery surveys on two products that use impedance monitoring laboratory design and commercial design, and found that the accuracy of both is more than 50%. A basic difficulty is the accuracy problem of measuring small variations. The normal 300-time time of the spare current is only at a magnitude of 0.25 × 10-3 ohms. Therefore, small and meaningful resistance variations may not be observed. In the following operating environment, the problem is more serious.
1) Interference caused by "noise" and floating voltage fluctuation during online measurement.
Be
2) The effect of corrosion crack on the internal resistance is highly directional, and the internal resistance value is relatively unsatisfactory to the fracture parallel to the current direction.
Be
3) Changes in electrolyte concentrations, which will continue to interpret results.
Be
Although the internal resistance measurement method is difficult to accurately measure the capacity of the battery, the internal resistance / capacity correspondence is difficult to revert, but for BMS, the internal resistance test is only used for the comparison between the battery cells, and the computer can be The change of the resistance is recorded and data processing to prevent battery capacity attenuation and fail, therefore, the internal resistance test is one of the key technologies for BMS.
For the measurement of internal resistance in the case of offline or battery openings, the excitation current loop and the voltage measurement circuit can be easily connected to the cells in the battery pack, but it is difficult to solve the incentives for online measurement. Measurement problem.
At present, most of which are parallel from both ends of the battery pack because there is a charger and battery pack, and the charger needs to be stopped, and the current change and voltage change of the battery are simultaneously synchronously, it is difficult to handle sampling interference.
With the excitation device of the midpoint, since the current adopted incentive internal resistance test apparatus applied at both ends of the battery pack, since the current is connected, the current is tapped through the middle tap after the upper battery pack. And the lower battery pack reaches the positive and negative electrode of the battery pack, eliminates the parallel influence of the external charger and the electricity load of the battery pack, producing a stable current excitation on the battery, and can accurately test the internal resistance of the battery.
2, system structure
The configuration of the valve-controlled lead-acid battery (VRLAB) in the general system is generally:
500kV substantial DC system: 2 sets of full capacity batteries, 3 chargers.
220kV substantial DC system: 1 set of full capacity batteries, 2 chargers.
110kV substantial DC system: 1 set of full capacity batteries, 2 chargers.
Mainly 108 2V, 18 or 19 12V batteries. The installation of the battery is also very different, and the distance between the battery and the operation is uncertain. Be
The BMS consists of a control unit, a measurement module, a related software, and auxiliary components, and a control unit can access multiple measurement modules to complete monitoring management of multi-sets of batteries of different only and different voltages. Control units are used for data transmission, data processing, and human-machine interface control, with RS-232 connecting interface and RS-485 remote (centralized) management interface, measurement module control interface, operation keyboard, display panel, sound and light alarm and alarm output Control contact. The control unit displays battery data in real time, intelligent analysis data, and timely alarms the operation of abnormal battery.
The measuring module is used for the inspection of battery data, and the built-in CPU is independently high-speed, in addition to regular voltages, current, temperature, etc., which can be accurately online to test the internal resistance after connecting the internal resistance test module. The measuring module is mounted near the battery, communicating with the control module, facilitating the on-site wiring installation.
Be
System structure box
3, the parameter setting of the system
As a complete monitoring system, the BMS system should first be used in DC 220V system, DC 110V system, DC 48V system, and DC 24V system, and consider its versatility, main monitoring module and internal resistance detection module are common For different systems, only the number of different acquisition modules is required, and the number of batteries of each acquisition module is set. Therefore, the system needs to set the following system parameters and alarm parameters:
1) Number of acquisition modules
2) The number of batteries collected by the minimum number of collected modules
3) Background communication address settings
4) Background communication baud rate settings
5) Battery group floating charge voltage upper and lower limits
6) Single battery floating charge voltage upper and lower limits
7) Internal resistance threshold
8) Capacity alarm
9) overcurrent alarm
10) Temperature abnormalities
The first four items are set for system, and the last six items are set.
4, voltage, current inspection and data analysis
The initial battery monitoring device only detects the end voltage, current, and temperature of the battery pack, and gives the alarm prompt with the detected data and the set upper and lower limits. The battery inspection instrument can be measured for each battery cell, and the floating voltage is over-limit alarm.
Most battery manufacturers placed the voltage measurement in the first position. For batteries in a floating state, the subtle difference of the floating charge can reflect the state of charge of the battery, and it can determine the serious failure of the battery because the floating charge is very Small, performance differences between batteries (mainly in capacity difference) is difficult to show. BMS monitors the complete working process of the battery, and the voltage, current, current, and different data processing methods are measured in real time, and use different data processing methods to improve the accuracy of data analysis.
The relationship between floating charge voltage and temperature can be compensated according to the slope provided by the manufacturer.
Vf = v0 + k (T-T0)
In general, k = '3' ~ 5mv.
5, residual capacity calculation
Attempting to measure the actual capacity of the battery in line through a method has always been the most urgent expectation of battery users, but so far, there is no such method or algorithm. Some introductions to calculate data or product advertisements in the battery, but the corresponding relationship between actual use data is not strict, and the internal resistance can only be used to distinguish the substantial change in battery capacity. In particular, the relative variation of the internal resistance can accurately predict the backward battery.
When the battery is in discharge, it is necessary to know the remaining capacity and power supply time of the battery. According to the rated capacity of the battery, it is not difficult to calculate the remaining capacity in real time, assume that the load is relatively stable, then the power supply time is converted. . Under normal circumstances, both the battery manufacturer gives battery capacity at different discharge signals.
Using the least squares method according to the discharge capacity of the battery manufacturer in different magnification, the relationship between the current and capacity can be simplified by the secondary curve, respectively, respectively, respectively, B, C:
6, battery running event record
On another aspect of BMS, the important role records running data in order to track when the battery fails, is determined because the battery quality is still caused by abnormal use. For long-term continuous operation, all data to record is not only high, but there is no practical meaning. The BMS design has an event generator, which stores the battery normally in the event form in accordance with the event production rules, which is stored significantly, and it is easy to query management. mainly includes:
1) The floating charge voltage is too high, too low
2) The charging current is too large
3) Excessive discharge current
4) The working temperature is too high, too low
5) internal resistance change
6) Depth discharge
Be
The event records the data and duration of the time. For battery operation characteristics of the power system, it is required to have a strong robustness of the event, which can shield the closing impact and measurement interference.
If there is an individual backward battery in the battery pack, the discharge capacity is determined by the worst battery.
7, remote management
Be
With the promotion of unattended substation, the online monitoring of batteries is more necessary. Battery monitoring equipment can be online, through remote management software, can view the current health of the battery and the recorded historical running event, timely knowledge of the alarm information issued by the monitoring process, decide whether to send people to maintain, or pass remotely remotely Perform a more step-by-step test.
8, measured data analysis
By testing the six different capacity of different voltage grades, the standard internal resistance adopts the Japanese imported single battery internal resistance test instrument, standard voltage adopts 0.1 standard digital multimeter test. Online measurement is measured by the BMS battery inspection, the specific data is as follows (the internal resistance unit is millio, the voltage unit is a volt):
Through test analysis, the BMS battery inspection instrument test is accurate, high, and it is fully able to compete for online monitoring of battery systems.
Fourth, small knot
Be
The battery is the core part of the power system, increasing the corresponding effective monitoring equipment, one hand to ensure that the battery works under reasonable conditions; more importantly, it is possible to take measures before the battery is completely failed to avoid it. Only the battery problem was found after power outage. Recommend: LiFePO4 Battery Manufacturer Energy storage battery Manufacturer Integrated machine energy storage battery series Manufacturer Lead lithium battery Manufacturer Outdoor Backup Battery Manufacturer Portable outdoor power supply Manufacturer Power battery Manufacturer Powerwall LiFePO4 Battery Manufacturer Battery rack Manufacturers Telecom LiFePO4 Battery Manufacturer Wall mounted battery storage Manufacturer China Lifepo4 Battery